The choice of production processes is a key decision for any enterprise engaged in production. This is especially true ofsmall batch production In the case where the Cost-effectiveness and qualityboth are critical factors in constantly changing market conditions. In this article we compare the small batch injection moldingand small batch metal and plastic cuttingto help you choose the right method, as a market player to achieve the most effective result and the best position.
Small batch injection molding: When to choose?
A small batch injection moldingis a highly efficient method for the manufacture of complex plastic parts. This technique is especially advantageous if the product has complex shapes, since injection molding is great for creating complex geometries. Another advantage is that there is a wide range of plastics available with different properties, so you can choose a material for almost any need. Products made by injection molding have excellent surface quality, which often does not require additional machining. The speed of the production process is also remarkable, and thanks to the short cycle time, larger quantities can be produced quickly. Although the initial tool cost can be high, in the long run, with a larger number of pieces, this method becomes extremely cost-effective. If an injection molding tool is already available, it is possible to try molding the product from several plastic raw materials, only the shrinkage values of the different plastic raw materials can influence the final size and deformation of the product.
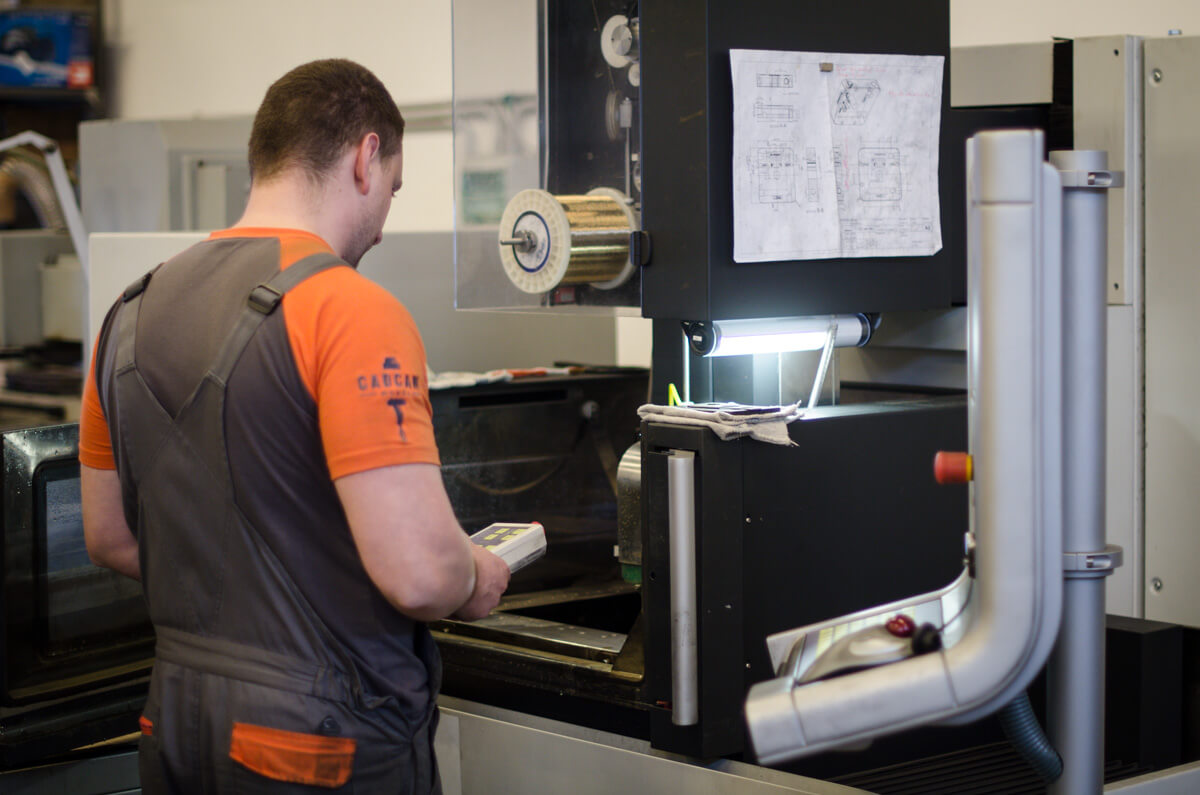
Small batch metal cutting: When is the best choice?
A small batch cuttingalso has many advantages and in some cases may be a better choice than injection molding. This method is especially suitable if metals or plasticswe want to machine a wide range, including special alloys. Cutting is an excellent choice for prototyping, as it offers a fast and flexible way to create custom pieces. If only a few pieces are needed, this technique can be ideal, as it does not require expensive tool production. Designs can be easily modified without the need for a new tool, which provides great flexibility in the manufacturing process. In addition, cutting allows the production of highly precise parts, which is essential in certain industries. In the case of plastic products, not all injectionable parts can be produced by cutting, if we think of a plastic raw material that does not hold the shape enough for the clamping force at different cutting holds.
Decision Points: Injection Molding vs. Metal Cutting
To choose the right method, it is necessary to take into account a number of factors. The number of pieces is a key consideration: Injection Moldingusually over 1000 pieces becomes cost-effective, while for smaller quantities, chipping may be preferable.
The material requirement is also decisive: it is necessary to decide whether a plastic or metal part is needed (eg: from a contact protection point of view, metal should not be considered). The geometric complexity of the product also affects the choice, since injection molding is more suitable for creating complex shapes. The desired surface quality, the production deadline, the available budget, and possible changes to the product design are all aspects that should be considered when making a decision.
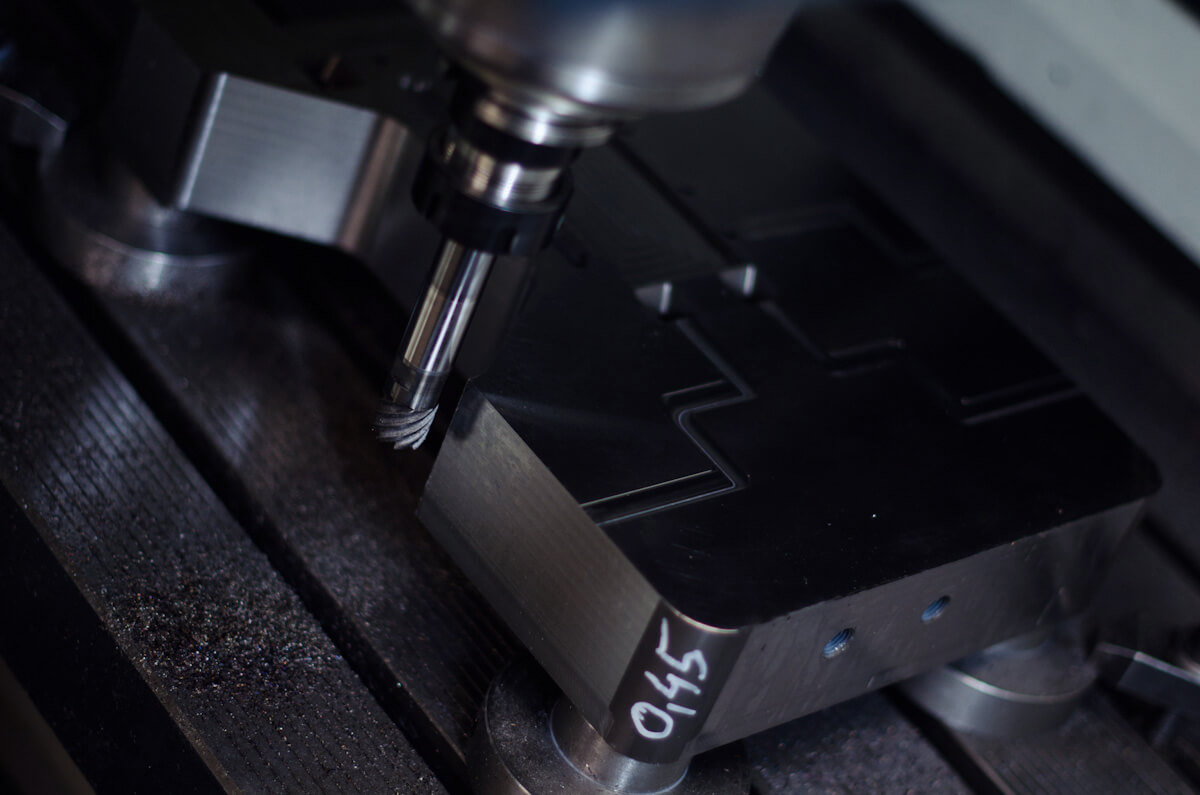
Summing up
All of the small batch injection molding, both a small batch metal and plastic cuttingcan be an excellent method under the right conditions. Injection molding is an ideal choice when complex plastic parts are needed in larger quantities, while die cutting can be the perfect solution for small quantities, precise metal or plastic for the manufacture of spare partsor Prototyping. When making the final decision, it is always necessary to take into account the specific requirements of the project and the opinion of the experts in order to achieve the best result, whether it beabout small batch injection moldingor for small series metal and plastic cutting.