The automotiveis constantly evolving, and vehicles include more and more plastic parts. These components not only play a role in weight reduction, but are also crucial for safety and performance. The Automotive Plastic Injection Molding Quality control is therefore critical during the production process. In this article, we will review the quality control processes and standards that ensure thatautomotive plastic parts comply with strict requirements.
Design phase and material selection
The automotive plastic injection molding quality controlIt begins in the planning phase. Engineers use simulation software to design parts and Injection Molding Processto optimize. These simulations help predict and eliminate potential problems before actual production begins. During the design phase, special attention is paid tothe choice of material, since plastics used in the automotive industrymust meet a number of requirements, including heat resistance, mechanical strength and chemical resistance.
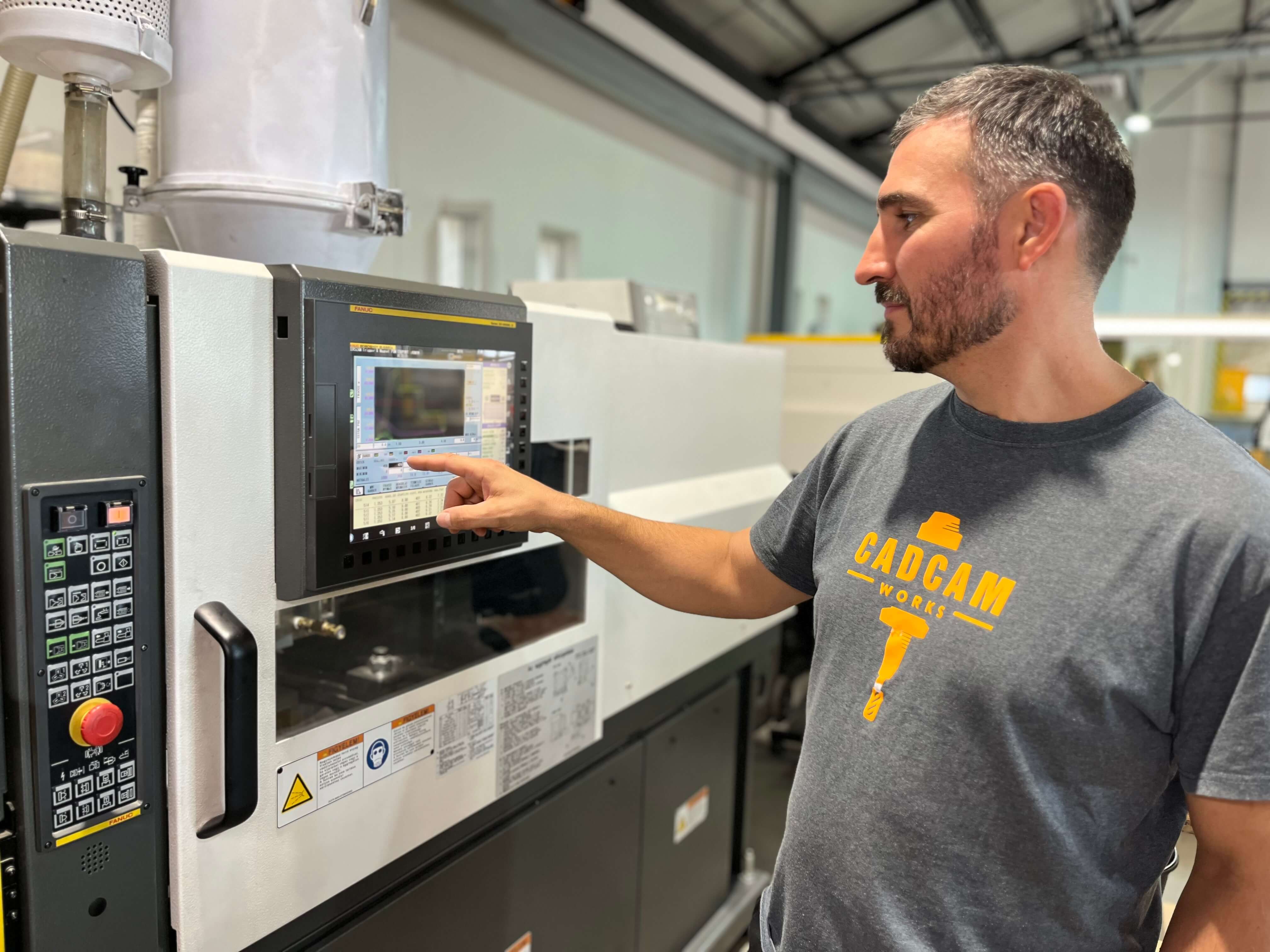
Production process and real-time monitoring
During the manufacturing process, automotive plastic injection molding quality controlContinuity is multi-stage. A Injection Molding MachinesIt is equipped with advanced sensor systems that monitor critical parameters such as temperature, pressure and cycle time in real time. This data is immediately analyzed, and in case of any discrepancy, the system automatically corrects the settings or sends an alert to the for quality inspectors. Finished parts undergo strict visual and dimensional inspection. In doing so, the surface quality and dimensional accuracy of the parts are checked using high-resolution cameras and 3D scanners.
Mechanical testing and traceability
The automotiveusedwith plastic partsIn contrast, the requirements for dimensional tolerances are extremely strict, often requiring micrometer precision manufacturing. In addition to size control, the mechanical properties of the parts are also tested, including tensile strength, elasticity and impact resistance. TheIn the quality control of automotive plastic injection molding, special attention is paid to traceability.Each production batch and even each part is assigned a unique identifier, which allows you to trace back every step of the production process. This is not only important for quality assurance, but also critical in the event of potential recalls.
Standards and environmental aspects
In the automotive industry, there are many international standards and regulations for the production and quality control of plastic parts. ISO/TS 16949 applies specifically to the quality management system of automotive suppliers, and also covers the key aspects of quality control of automotive plastic injection molding. In addition, theIATF 16949 standard, which is an addition to ISO 9001 for the automotive industry, imposes additional specific requirements on automotive suppliers. Environmental aspects are becoming more and more important in the automotive industry, and this is also affecting the production of plastic parts.Theautomotive plastic injection molding quality control It is necessary to take into account therecyclability andthe use of environmentally friendly materials. The The ISO 14001 environmental management system standard helps companies minimize their impact on the environment while complying with automotive requirements.
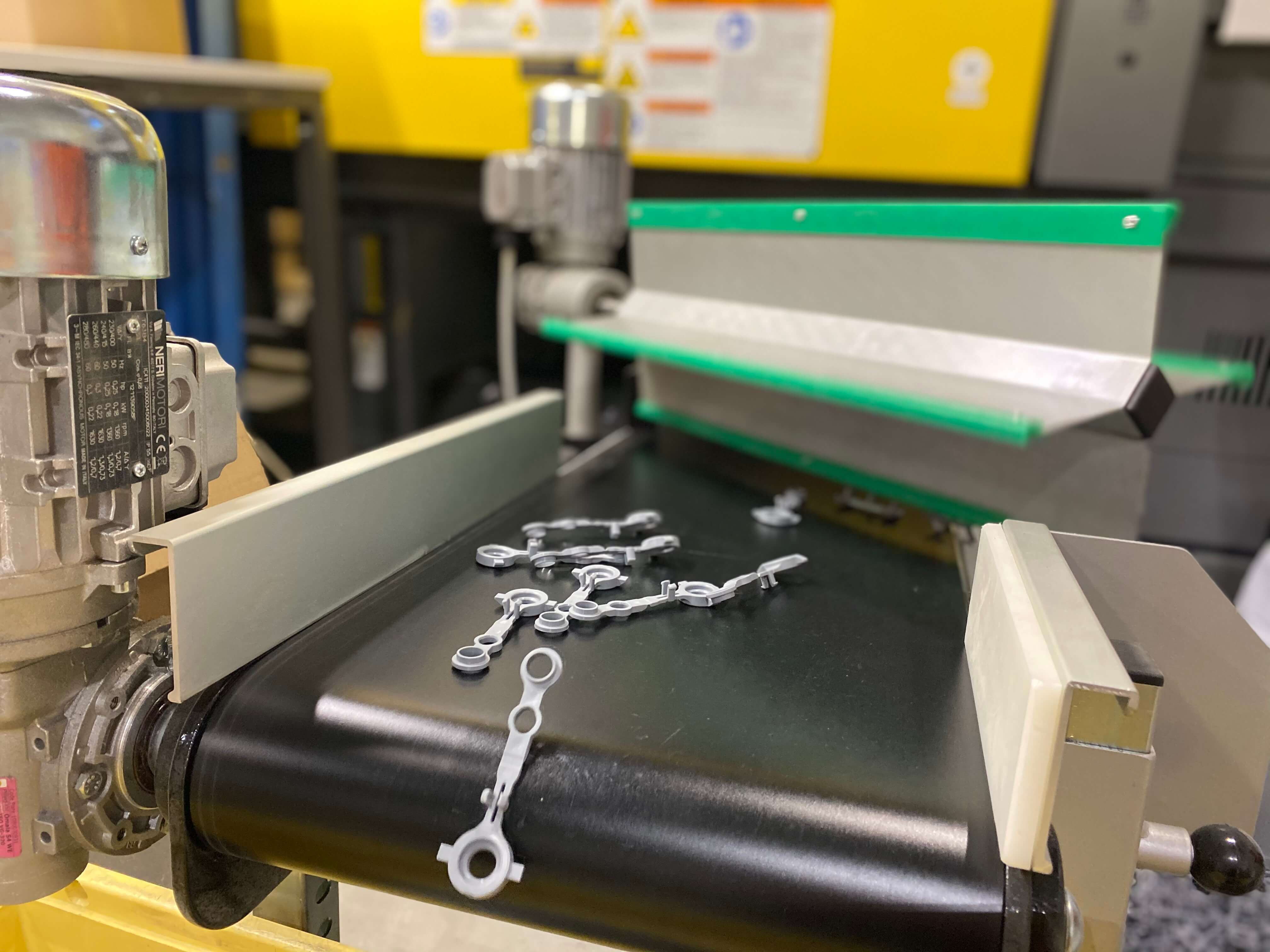
Summary and future trends
All in all, automotive plastic injection molding quality controlis a complex and critical process that ranges from design to final product inspection. Strict standards, advanced technologies and continuous innovation combine to ensure that automotive plastic parts meet the highest quality and safety requirements. With the spread of the concept of Industry 4.0, intelligent manufacturing methods are increasingly coming to the fore. The application of artificial intelligence and machine learning enables predictive maintenance and even more accurate quality control.The continuous improvement of quality control processes not only improves the quality of products, but also contributes to increasing production efficiency and reducing the environmental load. It is essential for the automotive industry that their partners, including plastic injection moulding suppliers, meet these high expectations, ensuring the safety and satisfaction of end users.