Proven ways to reduce production costs and increase efficiency
Plastic injection molding is now one of the most popular manufacturing technologies, as it is widely used, reliable and can be used to quickly produce large quantities of products. However, for many companies, plastic injection molding prices represent a significant item in the production budget. Therefore, there is a growing demand for solutions that can reduce production costs while maintaining quality and productivity. In this article, we have collected some useful tips that companies can use to optimize their injection molding processes and achieve significant savings.
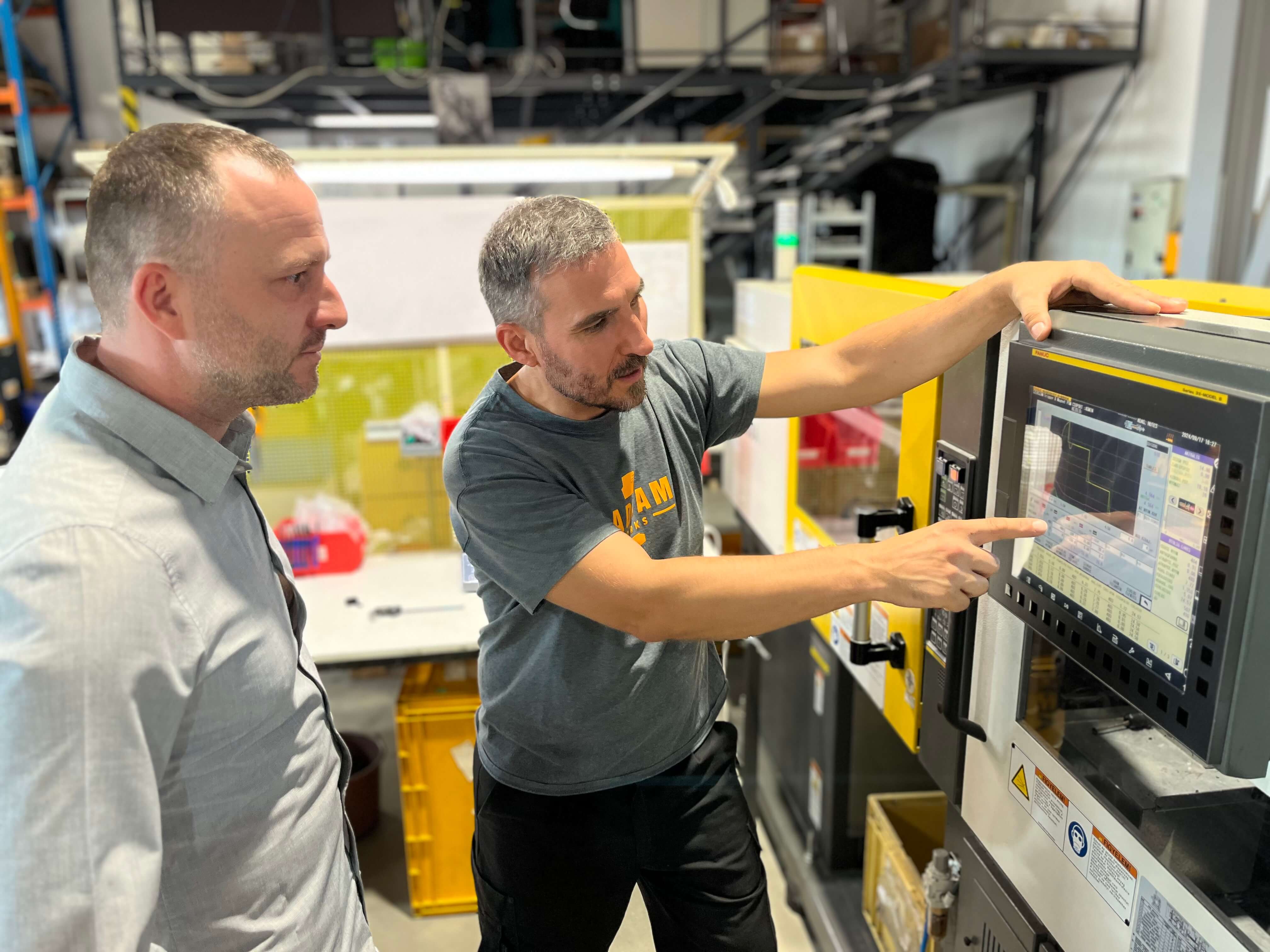
1. Optimization of material consumption: Thoughtful design
The first step towards cost-effective plastic injection molding is to optimize the design. The design of the product significantly affects the cost of production. Intricate shapes, unnecessary edges, thin walls or uneven wall thicknesses can increase the chance of errors and thus the scrap rate. This not only results in waste of materials, but also a longer production time. Therefore, it is worth enlisting the help of specialists already at the design stage, so that the design of the product is simple but effective. Less material consumption and faster production significantly reduce plastic injection molding prices.
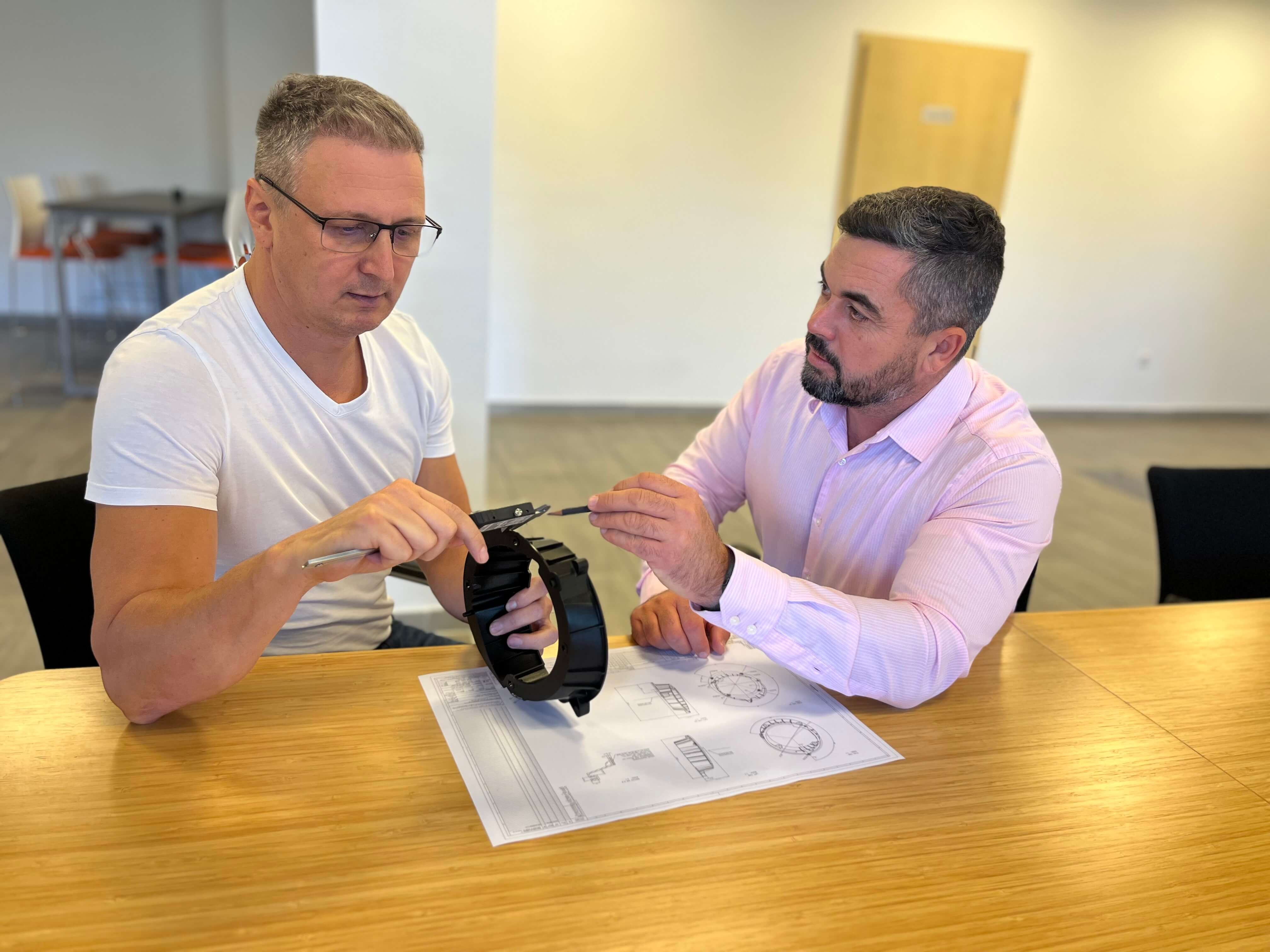
2. Smart choice of materials: Harmonizing quality and cost-effectiveness
Another important point is the selection of the right raw material. Although the price of different plastics may differ, it is not always worth choosing the cheapest raw material. A less durable or difficult to work material can even result in more scrap, which can ultimately make production more expensive. It is therefore important that the material used is not only cost-effective, but also has the appropriate properties for the given task. A good quality raw material can be more cost-effective in the long run, as it reduces the rate of defects and waste products and increases the life of finished products.
3. Preventive maintenance: Long-term savings with short-term investment
Maintenance of machinery and tools can also play a significant role in reducing production costs. Worn or poorly maintained machinery can not only result in defective products, but also slow down production. Therefore, it is important to regularly check the condition of machines and tools and carry out the necessary maintenance in a timely manner. With well-maintained machines, plastic injection molding will be faster and more efficient, so plastic injection molding prices will also decrease.
4. Fine-tuning machine settings: Creating the perfect balance
Optimizing cycle time is also a critical factor in reducing costs. Cycle time is the time it takes for a product to be made in the injection molding process. The shorter this time, the more products can be produced in a given time. To achieve the optimal cycle time, it is important to set the correct injection molding parameters, such as cooling time or pressure. In the case of modern injection molding machines, these parameters can be finely tuned, thus ensuring that the production process is as efficient as possible. With this method, plastic injection molding prices can be significantly reduced, while the quality does not suffer from a drop.
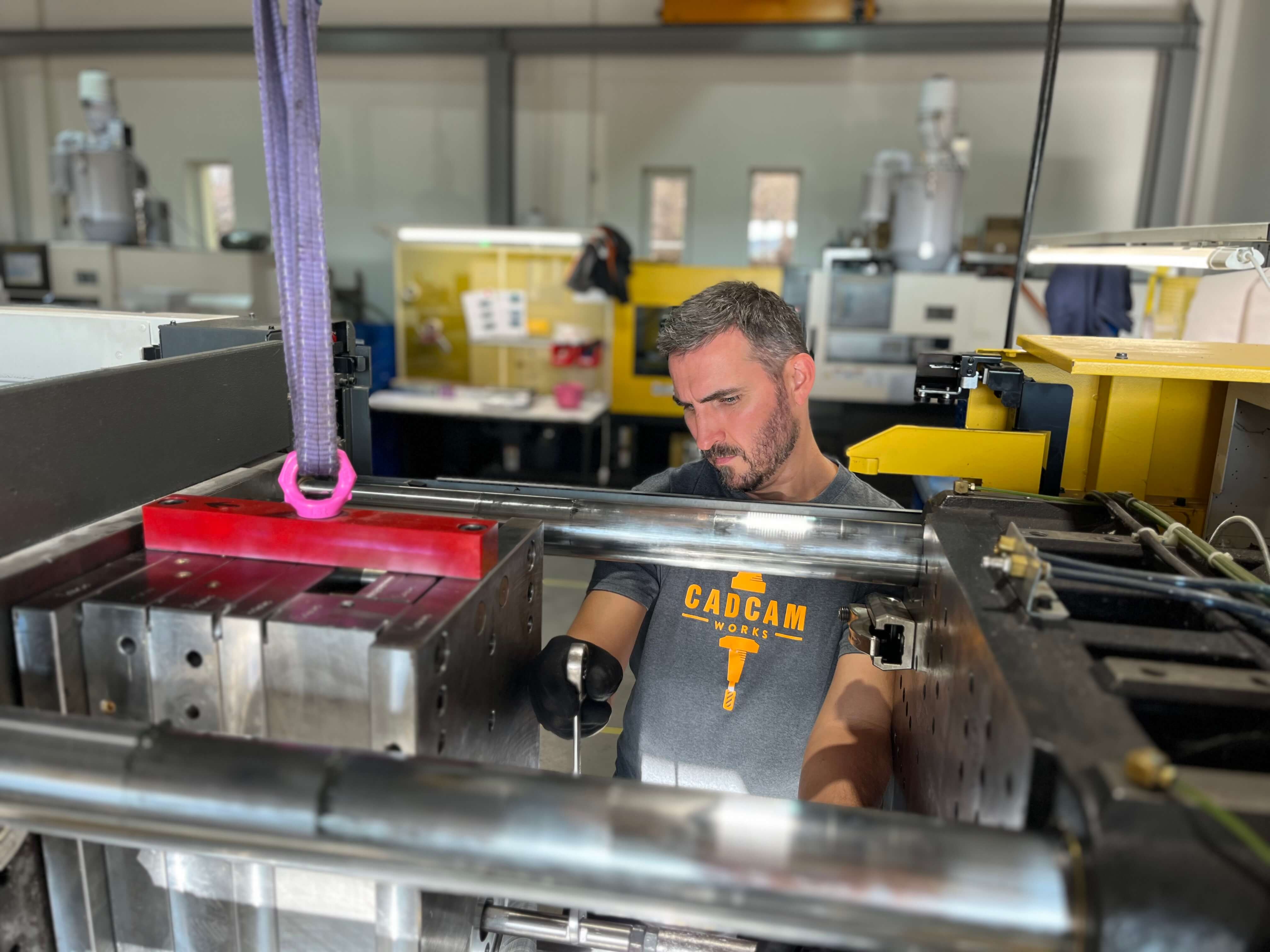
5. Optimization of energy use
Optimizing energy use can also help reduce production costs. In the injection molding process, a large amount of energy is required to operate the machines, so efficient energy use is a priority. The use of energy-saving machines or monitoring energy consumption during the production process can lead to significant savings. In addition, by optimizing production time and machine utilization, unnecessary energy consumption can be avoided, which also contributes to the reduction of plastic injection molding prices in the long run. All-electric injection moulding machines are becoming more and more common. Such machines are also produced, for example, by the Japanese factory FANUC.
6. Intelligent tool design: The cornerstone of efficiency
Tool costs also greatly affect the final price of plastic injection molding. Custom tooling can be costly to produce, but by optimizing tool design and using modular tooling, these costs can be reduced. Modular tooling allows the same tool to be used for the manufacture of several different products, so it is not necessary to make a new tool for each product. This greatly reduces the cost of production and contributes to making plastic injection molding prices more competitive.
7. Reasonable waste management and recycling
Last but not least, it is important to mention waste management. Recycling the waste and residual materials generated during the injection molding process is not only an environmentally friendly solution, but also serves to reduce production costs. The use of recycled materials can reduce the cost of raw materials while making the production process more sustainable. Through efficient waste management and recycling, not only plastic injection molding prices are reduced, but also the company's environmentally conscious image is strengthened, which can provide a competitive advantage in the long run.
Summing up
Overall, it can be said that reducing the cost of plastic injection molding can be achieved by coordinating several factors. Proper design, raw material selection, maintenance, cycle time optimization and energy consumption can all help to keep plastic injection prices competitive while keeping quality and efficiency intact.